Got Questions?
understanding Container Spaces FAQs
We are here to help you every step of the way. From design to delivery, we answer the questions that you have about the process of building with shipping containers.
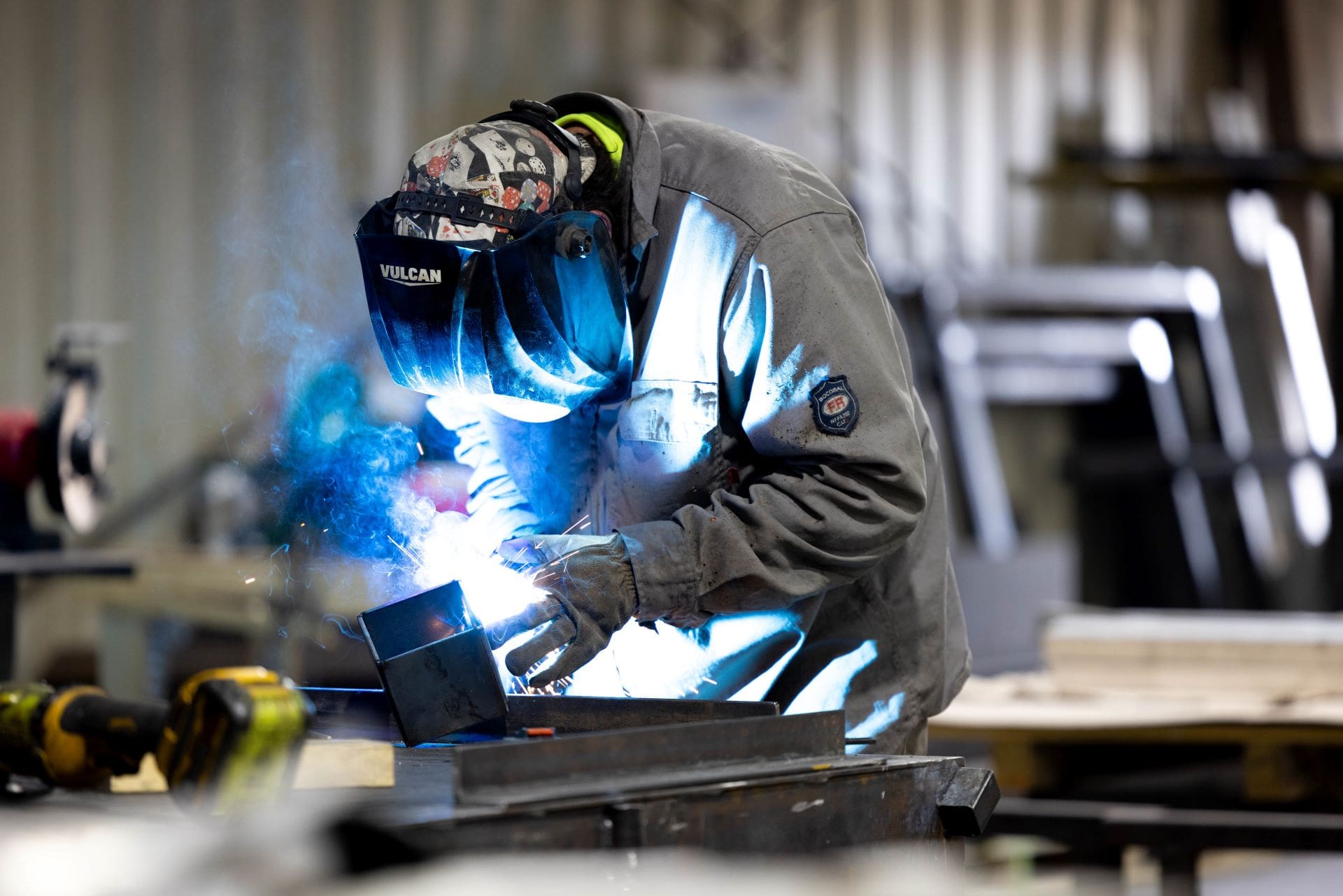
Frequently Asked Questions
GENERAL
We do not have a showroom like a car dealership would have. Every container home that we build is built for a specific customer and is already sold. Occasionally, we have a model home that travels to various shows. When the model is not at a show, we stage it at our facility, and it is available from time to time for tours by appointment only.
We do not accept walk-ins or non-scheduled visits. Prior to scheduling a visit, we need to know two specific things:
1. Do you already own property?
2. What your budget is for the container home (not including land)?
- Lead Time—This is the number of orders we have in line before we can start on your project.
- Production Time—This is the amount of time it takes to build your home once it enters production. It will vary depending on the floor plan and level of customization. For our standard floor plans, the production time is generally 65 to 90 working days.
As a rule of thumb, our standard floor plans, from order to delivery, is anticipated to be 4 to 6 months. Our custom floor plans can range from 6 to 18 months, depending on the complexity and level of customizations. CCL will provide an accurate completion date when a contract is issued.
Currently we offer two stacked floor plan options. Check out the two links below to view each model. We are always designing and planning for additional floor plans to offer. Keep checking in to see if we have added additional stacked floor plan options.
Our standard system is the highly sought after energy efficient, ecofriendly, Mitsubishi mini split system. These come in both standard (down to 6 degrees) and hyper-heat (down to minus 13 degrees) options. The number of indoor heads will be dependent on the floor plan.
We use closed cell spray foam insulation in the walls, ceilings and floor making each home we build very energy efficient. This not only provides the maximum efficiency, but it also reinforces what is already the strongest construction available.
All our floor plans come standard with an electric tankless water heater. There are many benefits to using a tankless water heater, listed below are just a few important benefits.
- Energy efficient
- Expanded life span
- Endless hot water
- Much smaller in size saving space
There are three different types of foundations we would recommend when preparing for your container home. (More details will be provided to your general contractor once you have selected which type you want).
- Piers: Digging and pouring concrete piers, then placing crushed gravel around the piers to allow for drainage.
- Piers & Slab: This option also includes pouring concrete piers and then a concrete slab over the piers to give a good solid surface under your container home; this helps keep things from digging under the home and washing it out. This is our most popular option and the option we would strongly recommend unless you are in a colder climate.
- Crawl space: This option would add a partial or full crawl space. If it is a partial crawl space, you can couple it with either the concrete pier option or slab. This is the option we strongly recommend in areas that have cold climates. The crawl space would keep all the plumbing connections and pipes from freezing.
** All these options are recommendations; you will need to check with the local jurisdiction to see if they have any requirements.
In the foundation there will be a steel embedded plates that will be installed when the concrete is still wet. This will allow us to weld your container home down to the foundation making it permanent and secure for years to come.
SHIPPING & DELIVERY
SHIPPING & DELIVERY
For those outside of the United States interested in purchasing and shipping their home, we can arrange to ship the finished container home to a U.S. port. Once the container reaches the U.S. port, all liability is assumed by the buyer/owner during the shipping to the final destination. If the final destination has different codes, we might not be equipped to build the container as our plans are based on the IRC codes. However, if the location does not have any codes or permits, or will accept IRC codes, then there shouldn’t be any issues.
Delivery is an important part of a successful experience start to finish. We have provided a list of requirements for what will be needed for a standard delivery fee.
- Roadways leading up to the property have at least 14’6” clearance from any low hanging objects.
- Entrance to your driveway is approx. 40’ wide and solid; we will be delivering with a semi. If the driveway entrance is not 40’ wide, then we need to make sure there are no ditches or dips on either side of driveway or on the opposite side of the road.
- The driveway and/or path to foundation is solid with compacted gravel or a hard surface so we don’t get stuck. It is the customer’s responsibility to let CCL know if the property is too wet for delivery.
- An open unobstructed area around the foundation is critical so we can straighten our semi with the foundation. We require approx. 150’ of almost level ground in the direction we will need to straighten out for unloading the home.
- The foundation is fully cured. If it is not, CCL will need permission from your general contractor to go back and place your home on the foundation.
- For a standard delivery make sure the foundation is not elevated more than 3” to 4” above grade.
If your site does not meet all these requirements, then most likely it will not qualify for the standard delivery fee, meaning some special equipment to complete the delivery might be required. In most cases, this means a crane will be utilized to pick the containers up off the trailer(s) and placed on the foundation. If you have any questions or hesitations, we would be happy to schedule a site visit. During the site visit we can determine the level of complexity and what special equipment will be needed. Most site visits range from $1,000-$1,500 depending on your location.
For more information on delivery please visit our “Delivery” Page.
Our delivery process is set up to make your life hassle free. We are the build team and the installation team supplying the truck, trailer, and tools to get your project delivered and installed safely. With each commercial project we collaborate with the owner/general contractor to arrange the delivery of each container to the jobsite. We will also coordinate the crane for placement, if a crane is needed. Once the containers are installed, our team will work to complete the items that we committed to finishing. Our goal is a completed project so that when we leave it will be ready for inspection. Please keep in mind every project is a little different on who completes certain items which is why CCL will coordinate with the owner/general contractor on the frontend to determine who will be responsible for those certain items.
Our starting price shown on each floor plan does not include the delivery and installation cost. Our delivery and installation costs are calculated on the “Start Your Journey” form or on the “Delivery“ page. It is particularly important to enter the correct zip code when prompted so the delivery distance is calculated correctly from Butler, MO. Once the form is complete, you will see a line item on the quote showing the cost for delivery and installation. Our standard installation would include welding down the container to the steel plates in the foundation, buttoning up any seams, utility connections from container to container if it is a multi-container home, and complete a final walk-through and cleaning. The final utility connections will be the responsibility of your general contractor.
COSTS & FINANCING
This is the most asked question. Our goal is to provide you with a realistic idea of what it will cost using the tools we offer on our website. Each floor plan offered will show the base price and the items included in the standard package.
To get a complete quote, please visit the “Start Your Journey” section. This will prompt you to enter the information we need to calculate an overall price. Once the form is completed, it will provide a more complete price for what you have selected. When you decide to move forward with us, you have the option to place a small deposit and sign a contract to start the process. Any upgrade not found on the website will be priced on an individual basis.
Another common question asked is what is the delivery cost? When you complete the “Start Your Journey” section, it will calculate the delivery cost based upon the zip code you provided on the form or you can visit our “Delivery” Page to see the cost.
The Container Home movement is still relatively new, and financing options are evolving as lenders adapt to these unique structures.
Please note: Custom Container Living, Inc. does not offer loans or financing, and we are not affiliated with any of the lenders listed. These resources are informational only. We strongly recommend researching and comparing multiple lenders before making any financial decisions.
There are usually two types of traditional loans you should start with.
- Traditional home loan— (15 year or 30 year); This type of loan is often found through a mortgage lender and not so much your local bank. However, you could get a recommendation from your local bank or simply search online to find mortgage lenders. Once you have selected a mortgage lender that will lend on a modular/manufactured home then you should apply for a pre-approval letter. This is vital for your budget and your construction loan approval.
- Construction loan—In most cases you will work with a local bank that you have a relationship with or is local to the area of construction. A construction loan allows for upfront money to make the purchase of the land, home, site improvements, etc. This type of loan allows for draws to be taken throughout the construction, paying for the progress from start to finish. Typically, once the home is near completion, you would contact the mortgage lender you received your pre-approval letter from and start the process of rolling the construction loan into a permanent mortgage of either 15 years or 30 years. They can best direct you to how this works.
COMMERCIAL
We have found there is not an out of the box one size fits all when it comes to commercial projects due to the size, purpose, site limitations, codes & zoning, and etc. When you are ready to explore the possibilities of using containers for your project, we are happy to help determine if it is feasible using containers and if it makes sense financially. Containers do not fit all project types which is why we try to learn as much about the potential project to help provide solid advice and direction. As much as we would love to accept every commercial project, we also understand containers do not make sense in some circumstances. When you are ready, please use the “CONTACT” page to send your information or email us at contact@customcontainerliving.com.
It is well known that you can use many containers to construct many types of projects. You can use containers to achieve many things such as: workforce housing, transitional housing, student housing, restrooms, and more, which is why we are here to help you understand all the possibilities and benefits of using containers for your next project. If it makes sense to use containers for your next project, we can build as small as you need or as large as you need.
RESIDENTIAL
A huge benefit is the peace of mind that each home is built to a proven building code making for a safe and sound home. All our certified containers are constructed to the International Residential Code. Another benefit is having a certified plan when applying for your building permit. The local jurisdiction knows it has already been reviewed and approved to meet the state building and safety codes.
The process of buying a container home can seem like a daunting task, but don’t worry. We’ve got you covered. Please review the “How It Works” section for some pointers in making the process easier. If you have any questions or need more information throughout the process, we are here to help.
It is well known that you can use many containers to construct a new home, however, we offer a variety of homes ranging from 160 sq. ft. to 960 sq. ft. It is very possible to build your home with more containers than what we offer within any of our standard floor plans, however, our standard floor plans are either state certified or ready to be state certified as a modular built container home.
If you desire to build a custom home, then the local city or county may require permits. We would then need to go through the process of getting your custom design state certified which can take extra time and be more costly. If your local city or county does not have permit requirements it will make the custom build process less difficult with a quicker turnaround. We look at each custom plan on an individual basis to determine if we can build it or not.
We use the most common container sizes which are 20’ and 40’ in length and 8’ wide. They have a “standard” height container measuring 8’6” tall and they also have a “high cube” measuring 9’6” tall. All our floor plans, whether a single- or multi-container model, will be built from a 20’ or 40’ one-trip container. Our smallest floor plan is 160 sq. ft., while our largest floor plan is 960 sq. ft.
Currently we offer two stacked floor plan options. Check out the two links below to view each model. We are always designing and planning for additional floor plans to offer. Keep checking in to see if we have added additional stacked floor plan options.
While shipping containers were made to be easily transported, they are not conducive to placing on a trailer and moving around each weekend as some of the “tiny homes” you see on TV. Our homes are made to be transported, set in place, and stay put. This doesn’t mean that you could not easily move them to a new location should you have the need. This will require a call to your local tow company that has the proper equipment. This is not something you would do yourself on your own trailer.
Codes and zoning will differ depending on the state/city/county where the container home will be located, what it will be used for, and how it will be secured. In many counties and smaller towns across the country, there may not be any zoning which will expedite the construction process. Below is a list of steps we recommend:
Call the building/zoning department with your local jurisdiction and ask the following:
- Do they require a building permit for a new residential home?
-
- If so, what is required for the building permit?
- Some areas do not require a building permit.
If a permit is required be prepared to ask the next two steps.
- Do they allow shipping container homes?
-
-
- One thing to note is sometimes as soon as you mention shipping container homes, they might be apprehensive and say “No”, due to the fact that they have the incorrect idea of what you are asking. Please assure them it will be a state-certified modular home. If modular/manufactured homes are allowed, unless they have it written specifically as no container homes, then it should be accepted, if all other criteria are met.
-
- Find out minimum square footage?
-
- Some locations have a required minimum square footage, so if that is the case, please know what that is.
The utilities (electric, water, sewer) connect the same as a traditionally built house. Your main utility connections will be one ¾” pex water pipe, one or two 3” sewer connections, and a 2” LB mounted on the side of the house for your electrical service. We will work closely with your general contractor to provide any information they might need. CCL is not responsible for making the final connections from the home to the main utilities. This would be completed by your general contractor.
A common question we hear is “are we able to upgrade or add large windows and large doors?” We can definitely consider that; however, the strength of a container comes largely from the container walls and when you start removing larger sections, it requires additional engineering, bracing, and welding. If larger openings are desired, we will work with our engineer to make the modifications for the additional bracing and welding. The cost of having the engineer modify the drawings, as well as the cost of the larger windows and doors are priced on an individual basis.
In short: No. All our homes are fully complete when they leave our shop due to certifications and inspections that must take place during and after a build is finished.
OFF-GRID
The process of buying an off-grid container home can seem like a daunting task, but don’t worry. We’ve got you covered. Please review the “How It Works” section for some pointers in making the process easier. If you have any questions or need more information throughout the process, we are here to help.
It is well known that you can use many containers to construct a new home, however, we currently offer three off-grid homes ranging from 320 sq. ft. to 640 sq. ft. one and two bedroom. In the coming years we plan to expand our off-grid lineup with a few larger models.
Our off-grid floor plans come standard with a tanked water heater. The option for a gas tankless is available.
The short answer is yes, we would love to build the home you desire. When customizing one of our off-grid homes, a team member will work with you to understand what you are looking for. It is important that we build the home so it will function within its limitations of being off-grid. We strive to give the best off-grid experience possible, but there are some limitations for which we must account for. All the finishes that you see under the “Build a Quote” are based on our standard category floor plans. If you want to customize your off-grid home, it is recommended that you visit the custom category and walk through the “Build a Quote” to see what additional customizations we offer. Once you have your list of custom items, please contact us to further discuss.
Water: If water is not available through the city or a well on your property, you might have to haul in water through a local water hauling service or do it yourself. You also have the option of using the rain catchment system, but in the off seasons you might have to consider alternative ways to get your water tank full.
Sewer: If sewer is available through the city or you have a septic system installed on your property, you have the ability to order your home with a standard flushable toilet instead of using a composting toilet.
Electricity: Your off-grid home is designed to supply power through the solar system that has been installed. However, if you’re in an area that does not produce the needed power due to overcast sky, weather related, etc., don’t worry as you have a few options to consider:
1. We outfit each home with the ability to connect a generator to charge the batteries or power your home. The generator is not provided.
2. You could grid tie to power if that is available. The home has been prepared to accept grid power.
Start your journey
Have Questions? Let us help!
Ready to take the next step toward your dream container space? Contact our team today to learn more about our floor plans, pricing, and customization options. Discover how easy and economical it can be to create your dream space with high-quality solutions built right here in the USA.